In the middle of a hand-sanitizer shortage caused by the coronavirus pandemic, Johns Hopkins and Baltimore distillery Sagamore Spirit are working together to manufacture the disinfectant for use by the Johns Hopkins Health System.
The collaboration came together in less than 10 days, with Sagamore Spirit converting 100% of its distillation processes from rye whiskey mash bills to corn ethanol in support of the effort. Hopkins tracked down the raw materials needed per the guidelines provided by the World Health Organization and helped create the formula, said Drew Thorn, vice president of finance and operations at Sagamore Spirit.
"Hopkins has been a fantastic partner in this process, both on the logistical support and on the technical side," Thorn said. "Members of the Hopkins pharmacy team have been working directly with us throughout product development and have come to the distillery to assist with initial formulation and compounding."
With the first batches already in production, the sanitizer will be in the hands of caregivers at Johns Hopkins Hospital this week.
"We have been so gratified by the support we are receiving from the community, from businesses, from individuals," said Paul B. Rothman, dean of the medical faculty and CEO of Johns Hopkins Medicine. "This is a fantastic example of that. Kevin Plank and Sagamore Spirit understand the gravity of the current situation, and they have stepped forward in a major way."
The partnership started taking shape a little more than a week ago, according to Michelle Azotea, director of project management and implementation for the Johns Hopkins Health System Supply Chain. Pharmacist John Hill and the supply chain team set out to make hand sanitizer in-house, but that presented too many obstacles to be safe and viable.
"There are not many places across any of the Hopkins campuses that can handle a large volume of alcohol or flammable liquid," Azotea said. "Knowing that we were in a crisis but also not wanting to harm the health and safety of our employees, we started looking at a means to retrofit either our consolidated services center or to tap into some of the spaces either within our pharmacy compounding area or within our laboratory."
But in order to create the volume necessary to support the whole health system, the team would need to make around 4,500 liters a month—more than any facilities at Hopkins could safely handle, Azotea said.
That's when the idea emerged to approach Sagamore Spirit. News stories reported that distilleries were forgoing their normal operations in favor of temporarily switching over to the production of hand sanitizer. At the same time, Under Armour, also owned by Plank, was making news for its efforts to help during the pandemic.
"We'd been monitoring the growing need for a safe and effective hand sanitizer, while navigating compliance, production, and supply chain issues around ramping up our capacity," Thorn said. "When Johns Hopkins approached us, we were ready to help."
Azotea said the collaboration was underway about an hour after Hopkins contacted Sagamore Spirit. Sagamore Spirit's facility and its operations team are ideally suited for hand-sanitizer production, though the switch posed both regulatory and supply chain challenges, Thorn said. While the FDA and Alcohol and Tobacco Tax and Trade Bureau have clarified certain guidelines to clear the way for distilleries to directly produce the ethanol for hand sanitizer production, getting the right ingredients—ethanol, hydrogen peroxide 3%, glycerol 98%, and purified water—is a tall order, he said.
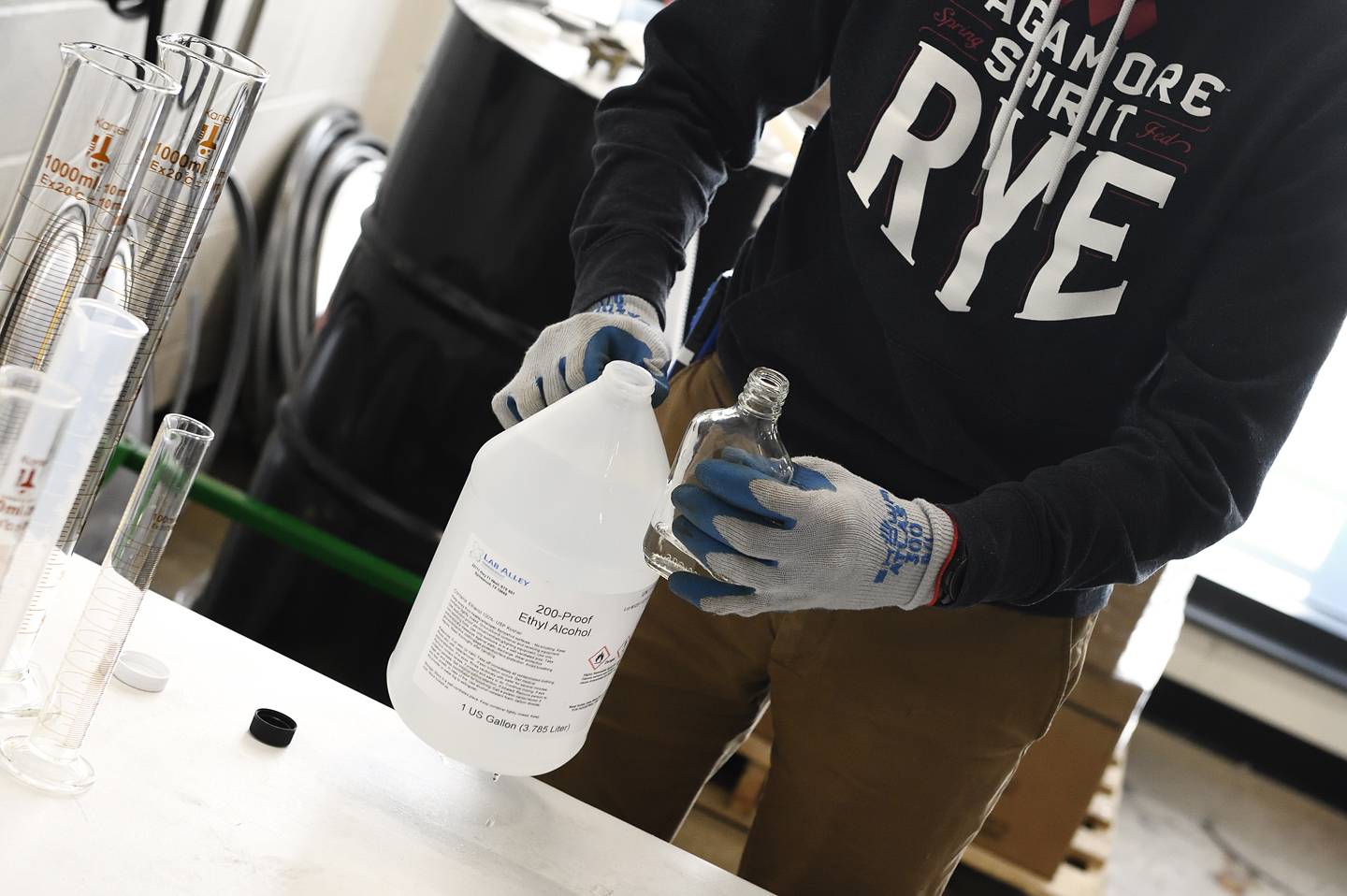
Image caption: The Johns Hopkins Health System helped procure the supplies for this massive production effort. Here, Sagamore Spirit Director of Operations Ryan Norwood pours a sample of the ethyl alcohol provided by Johns Hopkins.
Image credit: Will Kirk / Johns Hopkins University
"Aside from ethanol, we don't use any of the other ingredients in our normal operations," Thorn said. "To complicate matters, one of the biggest regulatory hurdles was that we weren't allowed to use our beverage alcohol in a nonbeverage product. So despite having a state-of-the-art distillery, we were having to go on the open market to buy ethanol, which has all but dried up."
Sourcing materials meant competing in the market with other health care systems looking to make the same production moves.
"Everyone is quickly trying to move to this distillery model, which has led to a different supply chain to try to obtain some of these raw materials," Azotea said. "We had to pull a lot of strings and do a lot of searching on the internet to try to find stocks available."
Hopkins tracked down the raw materials and Sagamore Spirit ramped up production, churning out its first batch of hand sanitizer the morning of Friday, March 27. On Tuesday, Sagamore Spirit delivered its first batches to Hopkins in 5-gallon buckets with spigots. Hopkins staff members transferred it to 4-ounce containers for clinicians' personal preparedness packs, as well as into larger containers for high-traffic areas, including security desks and nurses' stations.
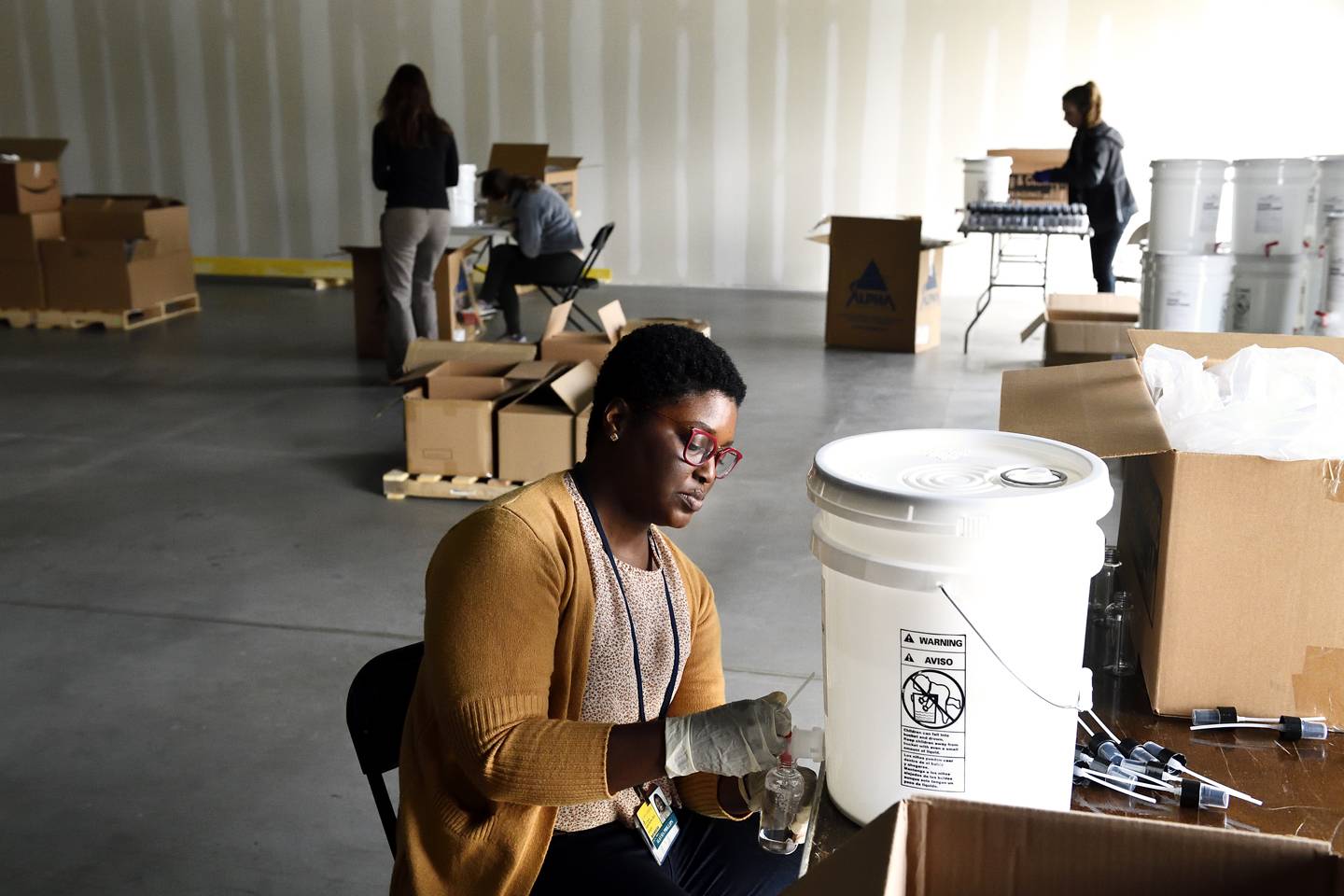
Image caption: At the Johns Hopkins Health System Consolidated Service Center, Alaysia Phillips from the Armstrong Institute for Patient Safety and Quality fills small spray bottles with sanitizer produced by Sagamore Spirit Distillery.
Image credit: Will Kirk / Johns Hopkins University
Both Sagamore Spirit and Hopkins hope to expand their homegrown partnership.
"We are open to providing hand sanitizer to the university and then also sharing the wealth and providing this to any other health partners or anyone outside of Hopkins if they need hand sanitizer," Azotea said.
Added Thorn: "We are committed to meeting Hopkins' needs. In addition, we are doing everything possible to expand production beyond 54,000 liters and support other medical systems and critical-need organizations throughout Maryland and beyond."
Tagged community, pandemic, coronavirus, ppe, covid-19, medical supplies