For months, the Whiting School of Engineering's full-service machine shop has served as Hopkins' in-house hub for personal protective equipment, cranking out 3D-printed face shields, ear-saver mask clips, and other equipment for the university's frontline workers.
But now, as campuses gradually reopen, the center will be ramping up their efforts to keep the Hopkins community safe, says Rich Middlestadt, director of WSE Manufacturing. Middlestadt and Niel Leon, senior staff engineer and WSE Manufacturing's design consultant, are teaming up with aerosol expert Ana Rule, assistant professor of Environmental Health and Engineering at the Bloomberg School of Public Health, to design and test a mass-producible respirator mask, much like the N95 masks that have been in short supply since the beginning of the pandemic.
"Our goal is to design a mask, comparable to the N95 respirator mask, that offers the same filtration capabilities and the same level of protection," Middlestadt says. "Effectiveness is our main concern, but we also want to keep the cost low. So if a company or other university wants to produce this mask, they could do it for only a few dollars per part."
3D printing is a popular strategy for producing PPE but is not ideal for a respirator mask, says Leon. That's because 3D printed materials are inherently porous, allowing particles to escape and potentially trapping harmful bacteria. Also, due to the rigidity of the plastics, 3D-printed masks don't seal tightly around the face. To create the shell of their new mask, the pair instead used vacuum forming, a manufacturing process by which a thin sheet of plastic is heated and pressed over a mold to create a part. A vacuum-formed mask offers key advantages: a flexible but airtight seal and easy sanitation between uses. It also costs less to produce, the engineers say.
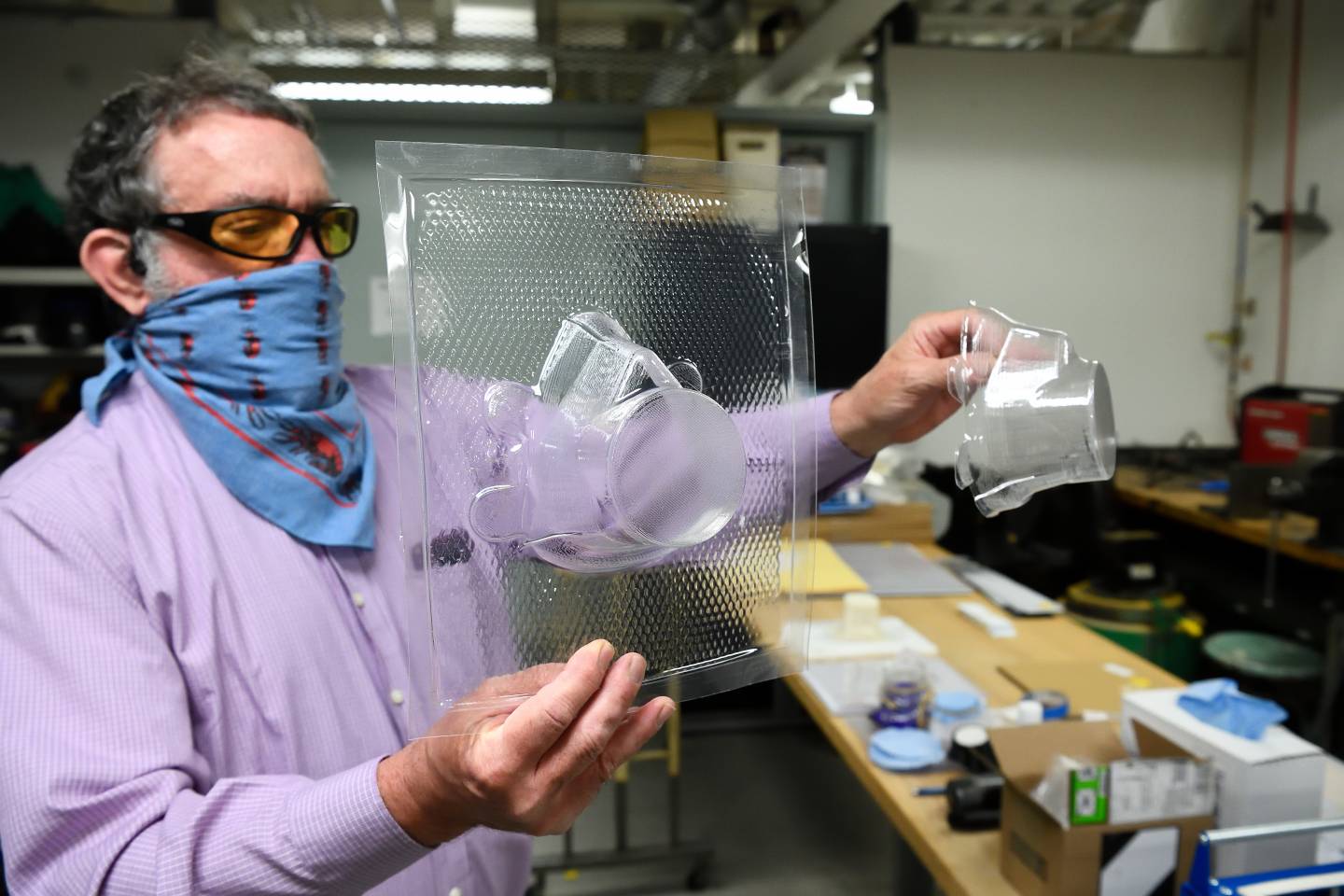
Image caption: Niel Leon examines vacuum-formed pieces built for WSE's respirator mask design.
Image credit: Will Kirk / Johns Hopkins University
N95 masks are engineered for one-time use only. So another advantage of this new design is its reusability. The filter, attached by a rubber band, can be popped off and replaced, while the rest of the mask is used repeatedly.
Still, the team knew that the biggest hurdle to creating such an alternative to the N95 mask would be acquiring material that could filter viral particles as effectively. According to standards set by the National Institute for Occupational Safety and Health, N95 masks must block at least 95% of airborne particles of a specific size.
At first, the team considered using the same material used in N95 masks, but found that pandemic demand meant the material was difficult to acquire in bulk. The solution then became obvious. They would just have to create an alternative filter material of their own, according to Anna Goodridge, who graduated in 2017 with a degree in mechanical engineering and is now an assistant research engineer in the Laboratory for Computational Sensing and Robotics and a member of the project team.
"The whole team started brainstorming commercially-available materials," Goodridge says. "One example is the air filters you use in your house's HVAC system. The higher the minimum efficiency reporting value rating, the better the filter is at trapping specific types of particles, so there's a lot to explore there."
Once Rule and the WSE Manufacturing team identified 12 possible materials—from furnace filters to regular old shop towels—the next step was to find scientists who could help them test the materials. They turned to the laboratory of Kirsten Koehler, an associate professor in the Department of Environmental Health and Engineering who is also an aerosol expert, specializing in exposure assessment methods to inform occupational and public health policy.
Filtration efficiency depends on several parameters, including the size of filtered particles. When we cough, sneeze, and even talk, we expel particles of various sizes, some of which are harder to filter than others, says Ashley Newton, a postdoctoral fellow in Koehler's lab who is performing the testing along with Goodridge.
"It's easier to filter out the relatively big and the relatively small particles, but the most penetrating particles, the most difficult to filter out, are those around 300 nanometers," Newton says. "That's the sweet spot we want to hit. If the material can filter out enough particles at the most-penetrating size, we believe it will perform equally as well or better for the rest of the particle sizes."
In addition to looking for high filtration efficiency, the environmental health and engineering team is also measuring if materials exhibit a permissible pressure drop; the ideal material will have a low drop in pressure, and won't require much force to get air through the filter. A material with a high pressure drop will make it too difficult to breathe—Newton compares it to breathing with a wet paper towel over your face. In the initial round of testing, none of the 12 materials met N95 standards. So the team is now testing these materials in combinations and layers, hoping to improve their efficacy. Once they identify an effective filter material, they will send results back to WSE Manufacturing, who will add the material to their mask prototype.
"Other people have designs out there for vacuum form masks, but at Hopkins, we have the data. We can robustly test every component of this mask, from how well it filters to how well it seals against the head and prevents leakage," said Middlestadt.
While Middlestadt envisions that his team could manufacture masks for Hopkins personnel who may need them in the coming months, his ultimate goal is to open source the design.
"Masks aren't going anywhere. The idea is that companies or universities across the country could make these for their employees if they have a vacuum forming machine, which many places do. We're using a cheap and available filter material to make a high-quality mask. Our design is something that anyone with the right equipment can manufacture."
Posted in Science+Technology
Tagged covid-19