For health workers in the field treating people stricken with Ebola and other diseases, a protective suit is the first defense against infection. The suit and head covering itself, however, can hamper the ability to help by impeding breathing, or heating up so quickly in high temperatures and humidity that workers can scarcely wear the suits for more than an hour.
Johns Hopkins University engineering students and team members hope to solve these problems as they improve a protective suit to be manufactured by DuPont under an agreement forged last year between the university and the international science and engineering company. Two Johns Hopkins mechanical engineering undergraduate teams, sponsored by the Johns Hopkins Center for Bioengineering Innovation and Design, or CBID, have developed prototypes for a more comfortable hood and face mask that make breathing easier, and for a battery-powered system that curbs humidity in the suit.
DuPont has licensed intellectual property for a coverall, hood, and full body suit designed and prototyped by CBID last year. Each product reduces the number of pieces required by current protocols, takes much less time to put on and remove, and cuts the number of potential contamination exposure points by nearly a third. The two recent projects by seniors at Johns Hopkins University's Whiting School of Engineering are meant to improve the CBID designs even further.
"The hope for us is this could be used for any infectious disease that's transmitted through bodily fluids," said Laura Scavo, who graduated in May with a degree in mechanical engineering and worked on the hood as a final project. Under a grant, she is continuing to work with the CBID team this summer.
"The aim of our device is to extend the working time of health care workers in an Ebola Treatment Unit by increasing thermal comfort, and thus decreasing the risk of heat-induced psychological and physiological impairments," the students who worked on the cooling system wrote in their final report.
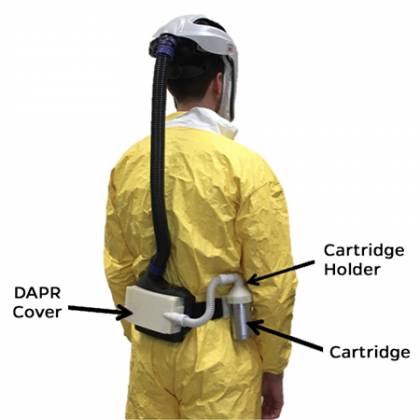
Image caption: A model wears the humidity-control apparatus featuring a Desiccant Air Purifying Respirator (DAPR)
Image credit: Johns Hopkins Center for Bioengineering Innovation and Design
Worn around the waist, the humidity-control apparatus adapts an off-the-shelf powered air purifying respirator and looks almost like something one would expect to see as part of a space suit. It includes a canister connected by a hose to a boxy fan unit, which in turn is connected with a second hose that runs up the wearer's back to the head covering. The system draws air in through the canister cartridge filled with a chemical drying agent, or desiccant. The desiccant soaks up moisture, delivering drier air to the person wearing the suit.
The project presented many challenges, some solved, some still in the works. The cartridge containing the desiccant had to be designed not to overheat due to the chemical reaction that occurs as the material absorbs moisture. In one laboratory experiment, the material overheated so fast that it melted a plastic container.
There was also the difficulty of sealing joints between the several pieces to create the most efficient airflow, and to keep out potential contaminants. That's still being figured out as the apparatus is tested and refined, but the team succeeded in key goals. The system significantly cuts humidity. The used desiccant cartridge can be regenerated with heating equipment commonly available at field treatment centers, and at 3.8 pounds the unit is well below the goal of 10 pounds.
In the hood project, Scavo improved on a model produced by CBID months earlier. Among other changes, she redesigned the integrated facemask to produce a good fit for a wide range of face sizes, adjusted filter placements so that the design would meet certification by the National Institute for Occupational Safety and Health, and worked with DuPont to develop prototypes for testing that could be mass produced.
Scavo and the team conducted field tests in Liberia this spring for the coverall and facemask. Feedback for refinements will be turned over to DuPont as the Johns Hopkins team pursues further grants to continue working on the project.
"A tremendous amount of effort has been put into this project by Johns Hopkins and DuPont in less than a year of development," said David Kee, North American marketing manager for Tyvek protective apparel, the brand name for clothing made by DuPont Protection Solutions. "DuPont is still evaluating the commercial viability of these enhancements; some innovations are conceptually appealing, but need further refinement prior to mass production. We look forward to our continued work together to strike the right balance and bring a truly innovative product to a wide market."
Posted in Health, Science+Technology
Tagged mechanical engineering, ebola, cbid