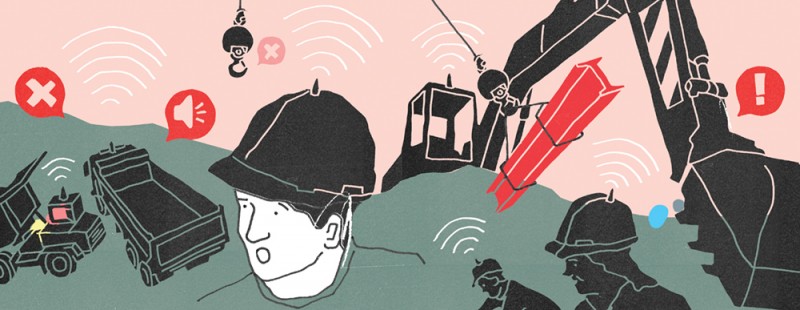
In man versus machine, the odds don't favor flesh on a construction site. One in 10 U.S. construction workers is injured each year, according to the most recent Occupational Safety and Health Administration statistics, and the industry witnessed 937 fatalities in 2015. The leading cause of death was falls, followed by struck by object, electrocution, and becoming trapped or compressed by equipment or objects.
Tony Dahbura, Engr '81, '82 (MS), '84 (PhD), an associate research scientist in the Department of Computer Science at the Whiting School, heard about such workplace risks from his son Greg, the owner of a demolition company in Hagerstown, Maryland. "He told me he was concerned about large construction vehicles—such as tractors, cranes, and front loaders—operating on job sites where workers are known to mill all over the place," says Dahbura, executive director of the Johns Hopkins Information Security Institute. "He said: 'Somebody is going to get hurt or killed. It's just a matter of time. Is there an engineering solution for this?'"
Determined to find one, Dahbura recruited students Stanley Ho, Engr '14 (MSE), and Sunyan Lee, A&S '15, Engr '15 (MSE), who were already working with commercially available Bluetooth-enabled beacon technology for his Computer Science Innovation and Entrepreneurship class. Together, they designed a system that uses low-power, wireless beacons embedded in a construction worker's hard hat. The beacon, the size of an Alka-Seltzer tablet, emits an electrical signal with a unique ID, like a lighthouse hailing its location to a passing ship. A sensor attached to construction equipment, such as a bulldozer or crane, receives the signal from any helmet within a roughly 30-foot range. When workers get dangerously close to a sensor-equipped vehicle, the driver is alerted by dots on a mounted display in the cab, not unlike planes on a radar screen. Dahbura says the alert can be accompanied by a siren or can disable the machine's operation.
The key, Dahbura says, is that these sensors can effectively see around walls, poles, and piles of dirt, thus eliminating the tremendous blind spots for these unwieldy vehicles. "The system can triangulate the signal to figure out exactly where the workers are," he says. "And the unique ID lets the operator know who is there, and how many."
Dahbura and a team of undergraduates are working on a prototype of the system, and they hope to finish this fall. If successful, Dahbura says, the invention can significantly reduce the risk of mobile machinery hitting workers, and save lives.
Posted in Science+Technology